Originally posted on Progressive Dairyman, by our very own Tom Woodall, CEO of Agri-Trac Inc.
An investment on a dairy barn floor should set the operation up for the future. However, a faulty floor can lead to costly losses due to down cows and lameness.
In some barns, there are many underlying and outside issues that can contribute to the chronic failure of every possible type of floor surface. Below is a checklist of issues to look for in a facility to troubleshoot problems and identify solutions in order to keep cows walking with ease.
Wear and Tear
When concrete floors become slick, a worn-down floor is often the first assumption. The truth is: It’s very rare worn-down concrete is the problem. Sand-bedded barns and areas heavily scraped by large equipment over many, many years will show wear on high spots.
The way to tell if this is happening is to wash the floor – if polished stones are visible, the floor is indeed wearing down (Photo 1).
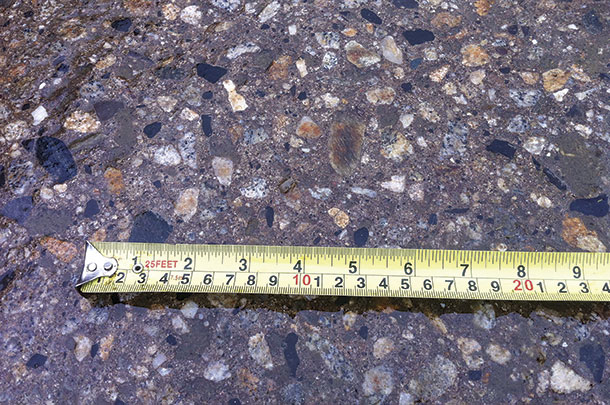
If you cannot see the underlying aggregate of the concrete, it means the original surface is still there. It may have lost its “grittiness” and be polished smooth, but it is not worn down to any extent.
Shallowed Grooving or Texture
Surprisingly, the floor is not worn down; it is filling up (Photo 2). There are many things that contribute to this problem; however, the use of lime on the cow beds is the number one culprit.
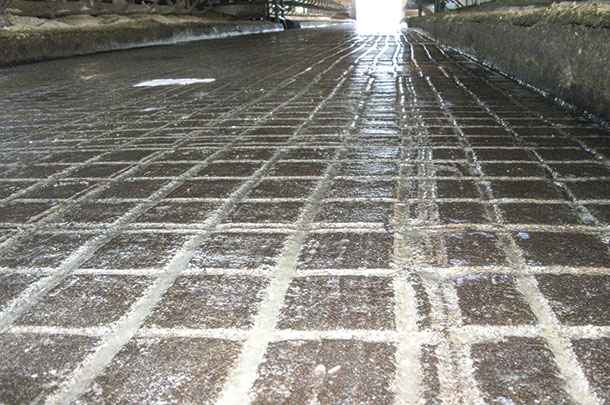
Lime is a 1940s fix for a 1960s barn. In the modern freestall facility, lime chemically and ionically bonds the minute it comes in contact with concrete. Today, there are better and more effective products available that do not cause this problem but, like anything, you get what you pay for.
Sometimes the cheapest product, such as lime, creates a higher cost somewhere else, like slippery floors and down cows. So how much was really saved?
Environmental Causes
Evaporation of liquids – due to ventilation, sunshine, wind and low humidity – will also cause minerals from the water source, urine, and manure to settle out and be left behind on the floors, thus compromising any grooves or texture. These minerals, such as calcium (lime) and sodium, are not easily removed. They bond to the floor, becoming almost as hard as the concrete itself.
Re-grooving (Photo 3) or traction-milling that removes the entire surface buildup (Photo 4) are the only solutions; it cannot be chemically removed or scraped out by hand.
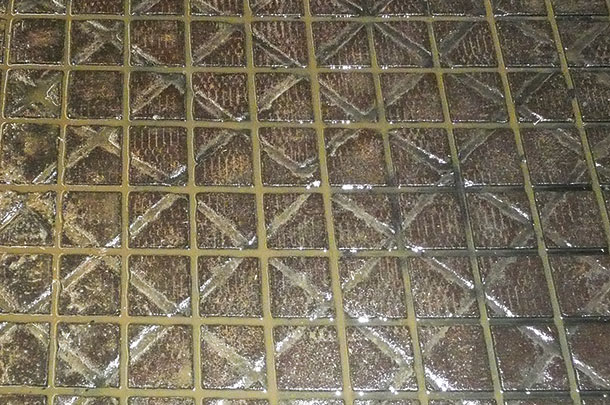
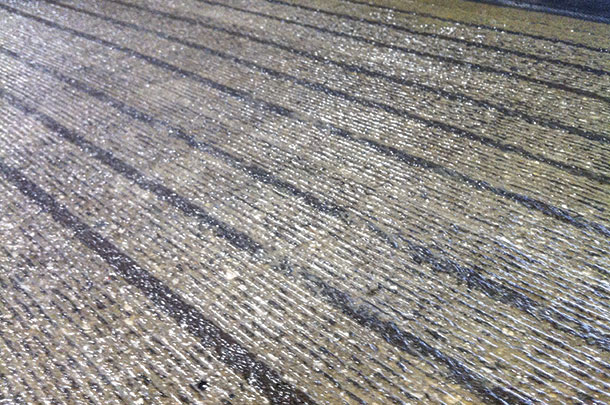
Algae formation in recycled wash water or moisture left standing in darker, less-ventilated areas will also create a brown, greasy film. This is more often seen in milking parlors and holding areas. A light acid or bleach wash several times a year will easily solve that problem. This will also work on milk solids and fats that create a slippery glaze on concrete.
Poor Maintenance
People will spend hours washing their tractors, trucks and combines to keep them functional – and also because the neighbors can see them. Not so much with a floor always covered in manure (Photo 5).
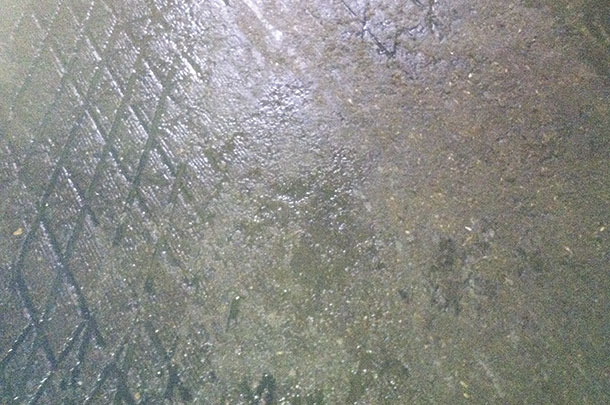
Who thinks to wash that down? The result can be a crusty buildup of manure not noticed under the slurry or in the sunny, breezy doorway. Once again, it compromises any form of traction in the concrete surface. Manure will stick to the ceiling if you let it, so why is anyone surprised it may be sticking to the floor?
Poor facility design
The modern freestall barn is designed around a liquid manure-handling system. Yet some designers and planners call for the separation of liquids from the solids where that combination is needed most: in the scrape alley. Sloping the scrape alley to the center and away from the sides has been the biggest problem in some regions for the past 10 years.
The liquids and urine drain away from the solids, which are then spread like peanut butter over the floor and dry out to form a slippery leather-like skin or, worse yet, a thick layer resembling particle board plywood (Photo 6).

It’s hard for any type of traction in the concrete surface to work when it is under a half-inch of that. Ultimately, the goal is a clean floor, not a dry floor. That can only be achieved by handling liquid manure as what it is: liquid manure.
Steep Holding Areas
There is an elevation difference between a milking parlor and the rest of the housing area of about 4 to 5 feet. It’s as if it was not thought about during the planning stages, and that entire elevation change is suddenly taken up in the short distance to the holding area from the scrape alleys up to the parlor. Cows don’t do well on steep slopes, especially where crowding occurs.
When designing a new facility, landscape planning is very important. Raise the elevation of the barn or lower the elevation of the parlor, office or milkhouse area driveways to reduce the holding area incline to a reasonable slope between the two areas of the facility or buildings.
False Expectations
Grooving a floor only one way works as long as the cows travel in that direction. However, one-directional grooving does little to stop a slip when the cow turns 90 degrees to eat or go into the stall or a crossover. Yes, it is half the price, but it only works half the time.
Something that modifies 10 to 20 percent of the floor surface is going to yield 10 to 20 percent improvement as compared to something that modifies 80 to 90 percent of the floor surface.
The goal is to stop the “slip” before it happens, not after it has started.
Slip-and-catch is not true traction, nor is it good for hoof health in controlling lameness. That said, a floor could be too rough. Years of extensive research and experimentation show there is a fine line between what is effective traction versus what is too abrasive on the hoof.
The floors in a barn are the most frequently used piece of equipment on the farm. Floors provide for cow comfort, cow traffic and manure handling every minute of every day for decades. Just like other pieces of equipment, flooring needs to be well constructed and maintained on a regular basis. Flooring is not the most expensive piece of equipment, but it can cause losses and expenses if not done or maintained correctly.